We use cookies to help us deliver and improve this site. By clicking Confirm or by continuing to use the site, you agree to our use of cookies. For more information see our Cookie Policy.
Reliable, leak-free pumping of hazardous fluids with sealless mag-drive pumps
23 May 2019
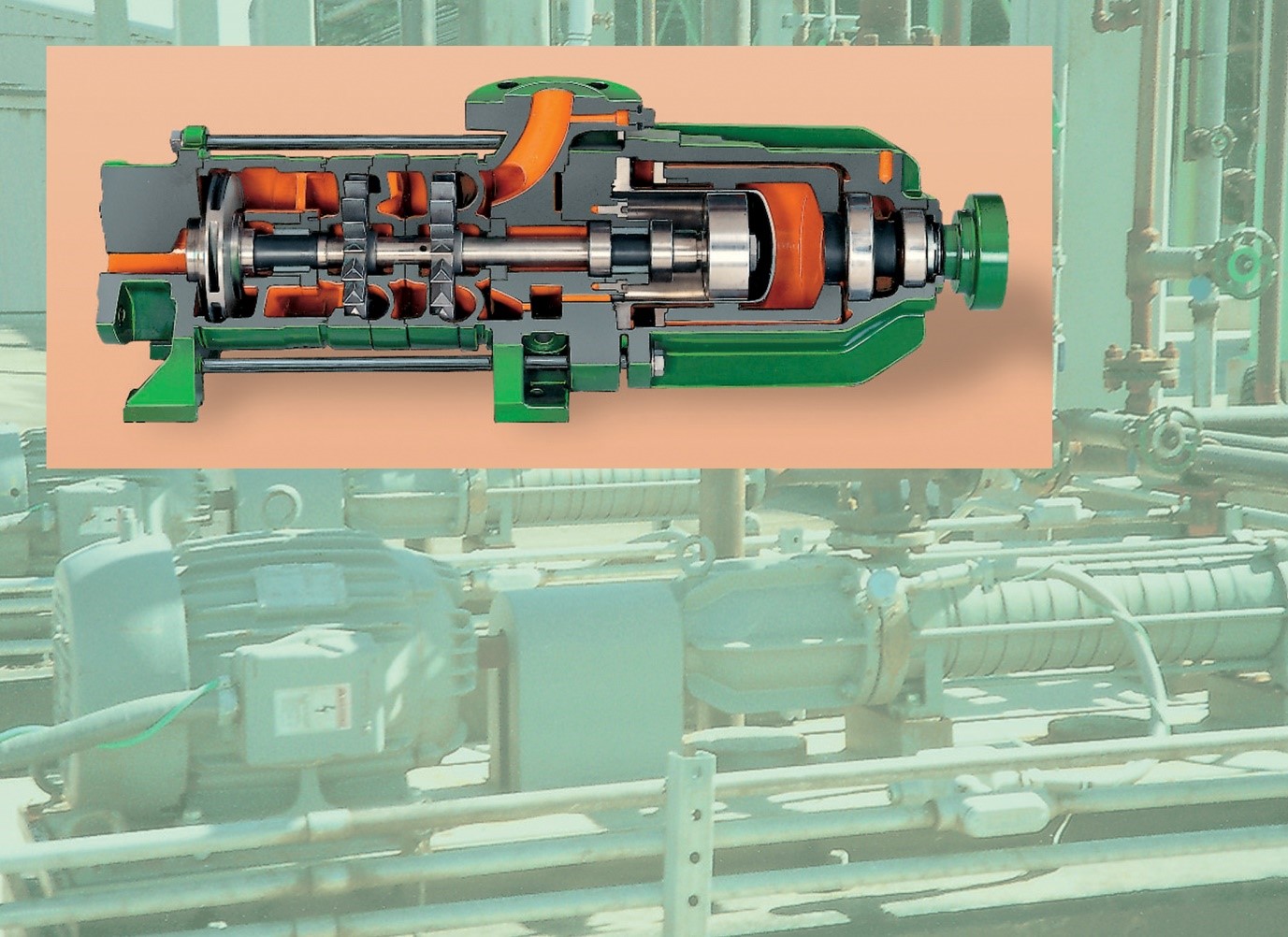
When fluids handling applications involve hazardous, flammable or corrosive liquids the need for robust and reliable leak-free pumps is crucial and in these situations Dickow SCM series magnetically coupled pumps are designed and built to excel. Available from UK pump specialists Michael Smith Engineers these self-priming, horizontal, side-channel pumps, operate more economically when pumping low capacities at high heads than standard centrifugal pumps.
Suited to pumping clean liquids without solids in the chemical and petrochemical industries, Dickow SCM pumps can handle capacities up to 37 m³/hr on fluid handling systems with differential heads to 400 metres and liquids at temperatures up to 180°C. They have a maximum operating pressure of 40 Bar, although a high system pressure option is available for applications with pressures up to 110 Bar. They are also suited to priming suction lines after filling.
The magnetic coupling and static containment shell design of these pumps results in a closed system which eliminates the need for double acting mechanical seals, external fluid reservoirs and any associated control equipment. With around 90% of pump failures caused by leaking mechanical seals, the sealless design brings the benefits of reduced costs associated with unscheduled repairs and maintenance caused by failing mechanical seals and therefore reduces the overall costs of ownership.
The single elements of the multipolar magnet coupling elements are completely encapsulated and not in contact with liquid and are made from Cobalt-Samarium for unlimited lifetime durability. Power is transmitted to the hermetically sealed liquid end by a bank of external magnets with the inner and outer magnet rings locked together by magnet forces which work as a synchronous coupling.
To achieve low NPSH conditions, the impeller on the suction side has an enlarged eye area while the rotating star-shaped side channel impellers are fitted in a chamber between the suction and pressure disk and keyed to the pump shaft in a floating position which eliminates the risks associated with excessive hydraulic loads.
The tight clearances between the rotating impeller and the stationary disks ensure superior self-priming capabilities along with high efficiency and high differential pressures to be achieved. Also, in applications where prolonged dry-running can be a problem, or when handling volatile liquids with low viscosities, the pumps can be fitted with additional SiC rings to avoid contact between the rotating and stationary parts.
The pump drive shaft is carried in anti-friction bearings which are rated for in excess of 3 years and grease-filled for life and protected against challenging environmental conditions by a radial seal ring. Options are also available which feature an oil-lubricated bearing bracket and close-couple design. The internal sleeve bearings are positioned in the pumped liquid with both the sleeves and the thrust bearings made from pure Silicone carbide which is highly resistant to corrosion and wear. Standard material for the stationary bearings is carbon, although Silicon carbide is also available. These features ensure long service intervals and reduce the chance of premature failures.
When coupled with Ex-drive motors Dickow SCM pumps can be used in hazardous area Group II, Category 2 situations and are suitable for sites which have increased safety requirements.
CLICK HERE FOR MORE INFORMATION ON OUR DICKOW RANGE OF PUMPS