We use cookies to help us deliver and improve this site. By clicking Confirm or by continuing to use the site, you agree to our use of cookies. For more information see our Cookie Policy.
Chemical Transfer Pumps & Chemical Dosing Pumps
Understanding the Basics of Chemical Transfer Pumps
Transfer pumps are an integral part of many industrial processes, specifically in the chemical industry where careful and regulated transfer of liquids is critical. These specialised types of pumps are designed to offer an accurate and controlled dose of a substance into a fluid stream, commonly known as 'dosing'. The precision and reliability of these pumps make them an excellent choice for an array of applications including water treatment, pharmaceutical production, and food processing.
A broader understanding of dosing pumps, especially in the context of chemical transfer pumps, reveals their unmatched utility and versatility. These pumps can handle a wide range of chemical fluids - both corrosive and non-corrosive. Whether in applications involving solvents, acids, or alkaline solutions, the chemical pump ensures a safe and effective transfer process. This highlights the role of these dosing pumps in driving the efficiency and safety of chemical dosing systems.
Delving into Chemical Dosing and Its Applications
Chemical dosing applications utilise finely tuned devices known as dosing pumps to precisely control the delivery of a specific dose of a chemical substance into a system. These substances, often corrosive in nature, need to be managed accurately to prevent damage to both the application system and the surrounding environment. Therefore, the functionality of dosing pumps is critical in industries such as water treatment, agriculture, pharmaceuticals, and manufacturing, where the precise mixture and distribution of chemicals can determine the quality of the end product or the efficacy of a process.
To accommodate the diverse needs of various industries, a wide range of chemical transfer pumps is made available. The complexity of fluid transfer within these industries frequently requires specialised equipment such as injection pumps. These are specifically designed to enable the transfer of substances into high-pressure systems effectively and safely. Chemical transfer pump design varies, from simplex single piston setups to multiplex plunger types, enabling a bespoke solution to particular chemical dosing requirements. Therefore, it is of utmost importance to choose the right pump for a given application, considering factors such as the chemical compatibility, required pressure, and the corrosive or abrasive nature of the liquid being transferred.
Exploring the Types of Pumps Used in Chemical Process
There is a wide range of pumps that are utilised in chemical processes, each with unique capabilities suited for different applications. Dosing pumps, for instance, are a specific type of pump designed to deliver precise quantities of chemicals, ensuring accurate and safe dosage during chemical production and transfer tasks. They are a popular choice among industries due to their ability to handle corrosive, abrasive, and high-viscosity liquids. Moreover, their compatibility with a broad range of chemical elements elevates their demand in complex chemical processes.
Additionally, magnetic drive pumps and centrifugal process pumps also play a pivotal role in chemical transfer processes. Magnetic drive pumps offer a seal-less design for leak-free performance, making them an ideal choice for handling hazardous and reactive chemicals. On the other hand, centrifugal transfer pumps are renowned for their high-capacity flow rates and ease of maintenance, essential features for bulk chemical transfers. Because of the diverse range of chemical pumps available, identifying the best fit for your process can be challenging. We encourage you to contact us, our professionals are ready to assist you in choosing the right pump for your specific chemical process needs.
Determining the Right Pump for Your Chemical Process Needs
In the sphere of chemical production, procuring the right pump for particular process execution is pivotal. The variety on the market is significant, from diaphragm pumps and centrifugal pumps to specific chemical transfer pumps, each adept in different aspects of the chemical process. When you need to buy chemical transfer pump, a determining factor is the type of liquids your operations frequently handle. Each pump has its unique specifications, thus, understanding certain properties of the liquids such as abrasiveness, corrosiveness, temperature, and viscosity ensures the longevity of the pump and supports efficient processes.
When you're dealing with liquid transfer in your chemical processes, considering factors such as chemical compatibility and low maintenance are essential. Not all pumps are designed to handle all chemical properties, so seeking a chemical pump that matches your liquid properties can avoid potential operational hiccups. For instance, diaphragm pumps are known for their robustness in handling abrasive and corrosive substances. Given their low maintenance need, they contribute to reducing the operational costs. Furthermore, pumps used in dose-centric processes need to have incessant precision, as even minor inaccuracies can lead to significant losses. Therefore, whether your operation involves simple fluid transfer or precise dosing, the right pump selection lays the groundwork for smooth-running chemical processes.
The Role of Centrifugal and Magnetic Drive Pumps in Chemical Transfer
In handling the complexities of the chemical industry, such as dealing with corrosive materials, solvent handling, and fluid transfer, the efficiency and safety of processes are of utmost importance. Considering this, two types of pumps have marked a significant presence in chemical transfer operations, namely centrifugal pumps and magnetic drive pumps. These pumps come with multiple benefits and capabilities, particularly well-adapted for challenging operations involving hazardous and corrosive substances. The right choice of dosing pumps can prove to be a game-changer, presenting an effective solution for your chemical process.
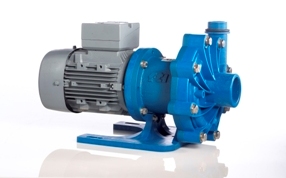
Plastic centrifugal pump for chemical transfer
Centrifugal pumps are renowned for their self-priming capabilities, providing a broad range of chemical transfer solutions. Conversely, Magnetic drive pumps also known as 'mag drive pumps', are known for their robustness against corrosive substances, making them an excellent choice for chemical dosing procedures. Additionally, these pumps are available in a variety of complyances, such as ATEX certified pumps, which ensures safe operation in explosive environments. If you are handling a range of chemical substances, Ltd's extensive inventory of process pumps can cater to your needs. These pumps ensure safe and efficient operation, even in the most challenging environments. For more information on our broad range of chemical transfer pumps, feel free to contact us.
Advantages of Using Low Maintenance Pumps in Chemical Production
In the chemical production industry, the choice of pumps bears significant implications on operational efficiency. Different types of pumps, such as the air-operated double diaphragm, magnetic drive pumps, metering pumps, and injection pumps, come with their distinct advantages. The right chemical transfer solution often involves a meticulous review on the application, environment, and liquid characteristics. Notably, low maintenance pumps offer great advantages over other types in this industry.
AODD pumps offer a simple and rugged solution for chemical transfer.
For instances where viscosity and abrasiveness are the primary concerns, air-operated double diaphragm pumps are typically used. These pumps can effectively handle liquids with high viscosity and abrasive nature without compromising on performance or uptime. On the other hand, magnetic drive pumps excel in handling volatile and corrosive liquids. Their gas-proof design and absence of seals minimise the risk of chemical leakage, thus contributing to a safer work environment. More so, magnetic drive pumps require less maintenance than the rest. Metering pumps and injection pumps also form part of this range of chemical pumps, providing precise control in chemical dosing operations. A stark representative of the intersection of functionality and convenience, these pumps augment the workability in demanding industrial environments. Furthermore, chemical transfer pumps come in different models and specifications to cater to the specific needs of individual applications. The respective perks and advantages of these pumps underscore their importance in shaping industrial efficiency.
Considerations When Choosing a Pump for Corrosive and Abrasive Liquids
When dealing with corrosive and abrasive liquids in chemical production, selecting the right pump is essential to safely and efficiently manage flow rates. For instance, when used to pump viscous fluids, a barrel emptying pump is often utilised. However, there are instances where liquids with entrained solids can affect performance. Therefore, pumps can be constructed from a variety of materials to handle such challenges - from various alloys to hard-wearing plastics, these can offer chemical resistance and durability.
One of the key factors to be considered when you buy a chemical pump is compatibility. It is imperative to select a pump that will not prove to be incompatible with your chemical solutions. In addition, when deciding on the right pump for applications requiring a chemical transfer, considering factors such as flow rates and whether the pump will typically be operated in full or empty states is critical. A low flow rate might be suitable for less viscous fluids, whereas more viscous substances might demand higher flow rates. Thus, identifying the right solution for your chemical application ensures optimal efficiency and productivity for your production processes.
The Importance of Chemical Compatibility in Selecting Pumps
In the realm of chemical manufacturing and processing, choosing the right solution for transferring chemicals is of prime importance. It is crucial to note that using a pump that is incompatible with the chemical substance it handles can lead to disastrous outcomes. For instance, using a pump made of materials that are resistant to the corrosiveness of Adblue might not exhibit the same resiliency when it comes to transferring hydrochloric acid or slurry. Therefore, it is essential to specify the right pump materials to avoid any mishaps.
A selection of pumps designed with a range of chemically resistant materials are available across the UK, specifically designed to transfer different chemical substances such as chlorine, intermittent toxic liquids, and others. The valves of these pumps are usually made of materials resistant to the specific type of chemical they are meant to handle. For example, one wouldn't use a pump crafted for hydrochloric acid in a chlorine environment. It is also worth mentioning that a spare pump is always a good investment, as chemical restrictions might require a temporary solution during regular pump maintenance or unforeseen breakdowns.
Unpacking the Range of Pumps for Fluid Transfer and Injection
In the vast sphere of fluid transfer and injection, urea, inorganic solutions, and transferring chemicals necessitate a range of pumps, each designed to address specific needs. The selection process therefore involves a careful evaluation of your requirements; whether you require a compact solution for transferring flammables or a robust system capable of handling viscous and volatile substances efficiently. A case in point is the vane pump. This pump, which can conveniently run dry without any damage, offers a viable option for aggressive chemicals, considering its design that allows for excellent suction lift capabilities and a capacity to handle containers even as small as 20l.
Interestingly, some pumps are capable of self-priming, making them particularly suited for handling corrosion and abrasion, notably in the management of inorganic solutions. Here, considerations around health and safety as well as temperature and concentration of the solution at hand are paramount. To optimise your processes and to ensure you're getting the right solution, it's essential to find a pump designed to minimise maintenance while offering maximum flexibility. The right choice of a pump does go a long way in streamlining operations, reducing costs, and enhancing overall productivity - factors of critical importance in any industrial chemical setting.
Enhancing Efficiency with the Right Chemical Transfer Solution
In various industries, the concentration of the fluid being handled greatly influences the service life and effectiveness of the pumps used for chemical transfer. This highlights the importance of selecting the right solution, as different applications require unique characteristics and features for maximum efficiency. For instance, the utilization of magnetically driven pumps, known for their low maintenance properties, can notably accelerate transfer processes and improve overall productivity.
When handling corrosive fluids, factors such as the brittleness of the pump's material merit special consideration. The pump must possess robustness against the physical strain imposed by highly concentrated substances to maintain operational longevity. This underlines the importance of effective synergy between the chemical nature of fluids and the materials used in the pump construction. Understanding how these elements interact can significantly enhance the efficiency of chemical transfer processes.
See our full range of pumps |
---|
Check out our Chemical Transfer Pumps on MSE Pumps |
Send us your enquiry |
Contact us |